Specialist retrofit refurbishment of automated welding equipment
We are problem solvers. Your problem is our problem, and we will have the solution. Spectrum Engineering Division have the industry’s best technical, mechanical, and electrical expertise to offer you unlimited engineering solutions.
We understand that old equipment out there in workshops are on their last legs, have become unreliable and dying a death. That’s where we come in. Some systems we have retrofitted and repaired are really, really big.
Examples include long bed longitudinal seam welders that are built and fixed into the buildings infrastructure, modified by the customer over the decades with the building built around some machines in some instances. Therefore it is not an easy task to just replace with a new system, which is why we get asked to come in and sort it.
Our Process
We would assess the current condition of the equipment, see where it is going wrong, recommend suitable upgrades, and carry out testing and certification in line with UK health and safety regulations.
We can refurb, enhance and modernise old machinery, in turn saving the customer from needlessly and hugely expensive new capital equipment purchases. The other major benefit of this upgrade solution service we offer is we prevent massive downtime due to new equipment lead time. So major costs savings and vastly superior lead time bonuses. Win win.
Refurbishment typically involves replacing worn and outmoded components with brand new, re-calibrate controls, install new safety systems such as limit switches and emergency stops, adjust and upgrade mechanical systems, and much more. This not only enhances safety and performance but also ensures compliance with current industry standards.
Our retrofitting goes a step further – we integrate new technologies such as digital controls, remote operation features, programmable automation systems, or even swap out and incorporate new welding processes to vastly improve efficiency. These upgrades can significantly improve precision, consistency, and increase output.
Telephone: 01246 205 267
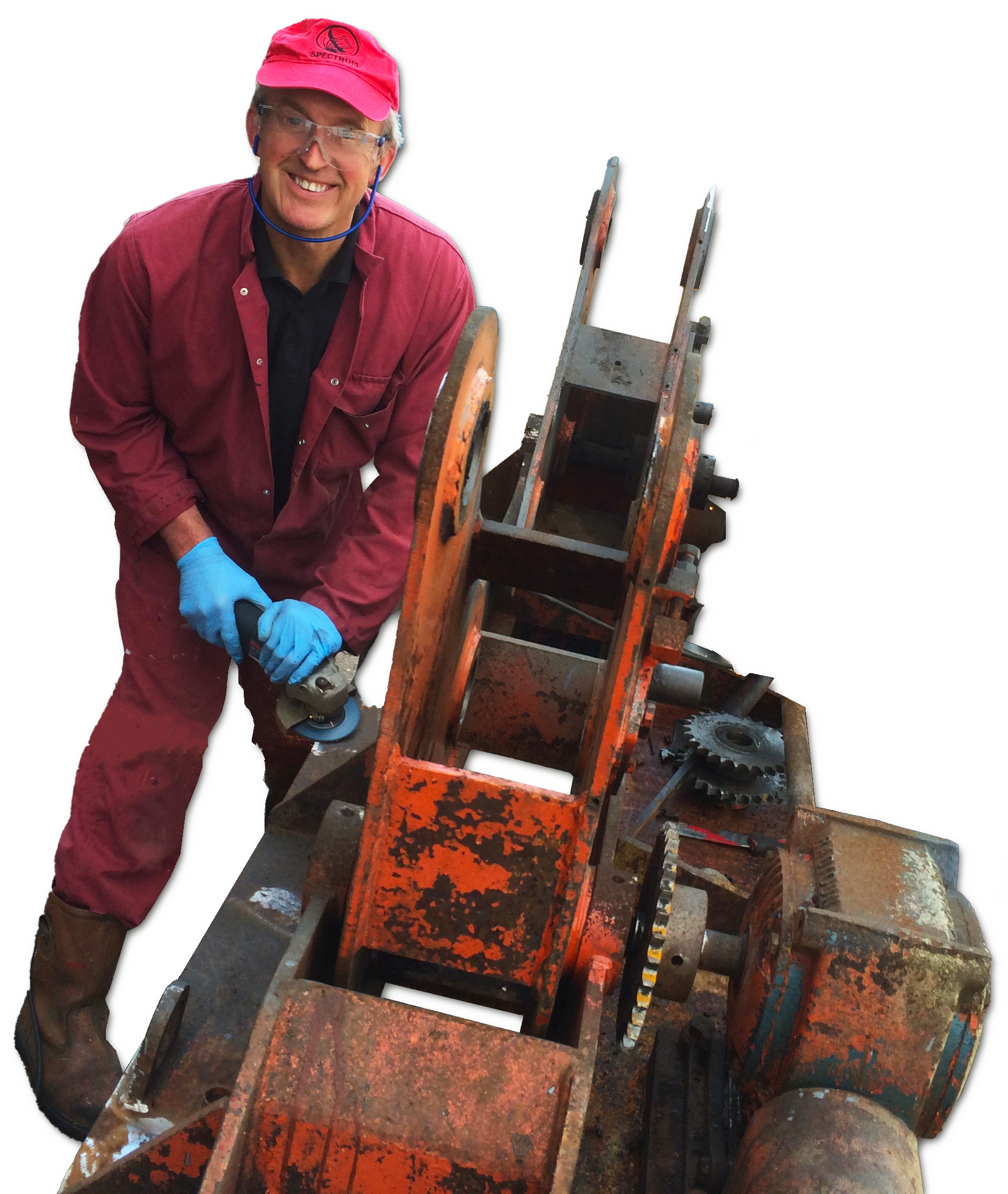
In house Capabilities
We also have in-house capabilities to design and build any inverter control panel system. This includes complex PLC automation control connected to any type of automation equipment, and integrate them into the computer system if this is needed. See below example case study of this.
To be more specific we can fully re-design, upgrade, modernisation, and improve any old pre-existing seam welder, beam gantry welder, positioners, rotators, robots and any welding or non-welding automation system. If you can think of it, we’ve probably worked on it.
We refurbish and retrofit back to better than brand new with custom work, tailored turnkey ideas, that can save customers vast amounts of money. Choosing to refurbish or retrofit existing welding equipment also aligns with sustainability goals, reducing waste and supporting the circular economy.
For businesses looking to maximise their capital investment and stay competitive, it’s an attractive option that balances performance improvements with cost control.
Refurbishment and Retrofitting Case Studies
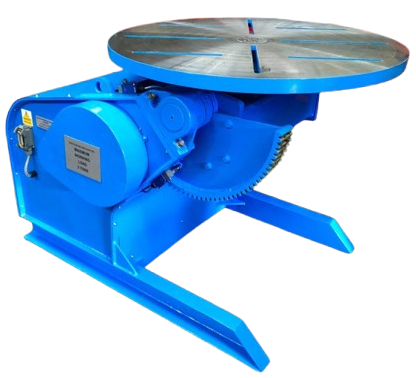
3 tonne positioner
We were asked to build a 3 tonne capacity welding positioner…. for a laboratory testing car engine efficiency at extreme angles. This machine was a precision engineered solution coupled to advanced PLC computer systems.
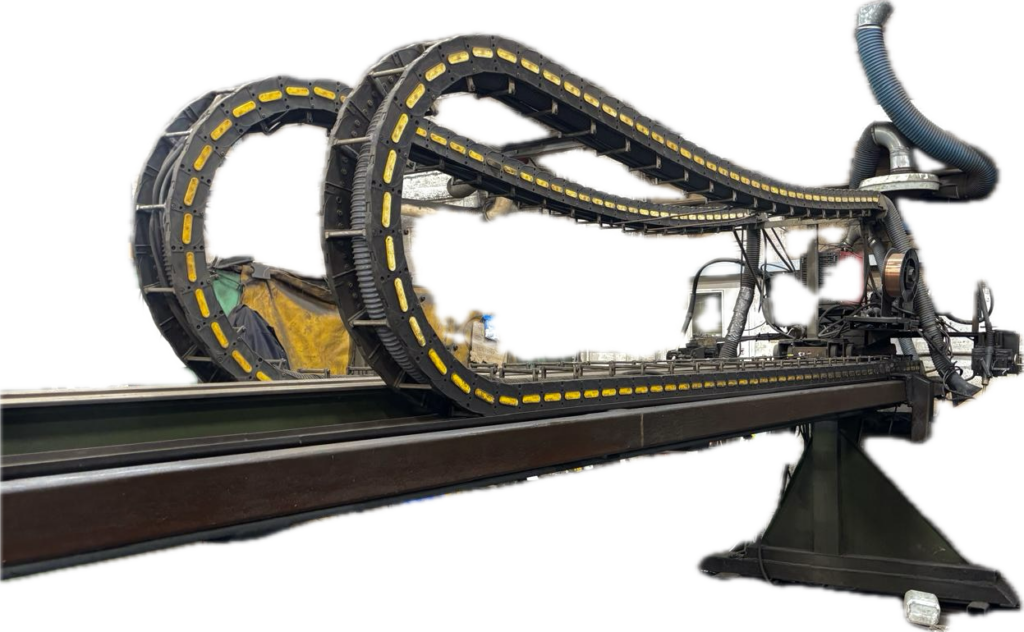
Tandem head MIG seam weld system
This was an old seam welder system with cables everywhere, an antiquated motor gearbox, that ended up cutting out and came to grinding halt in a puff of smoke.
More case studies to follow
Welding. It’s what we do.
Contact the UK’s smartest welding equipment supplier.
Telephone 01246 205 267.