Automation Refurb: Case study 1
Refurbishment and retrofitting a highly specialised 3 tonne positioner.
Service Level
- Discuss client requirements
- Meet the customer
- Site visit
- Problems addressed and solved
- Planning and design
- Specification
- Lead time (done within 2 weeks!)
- Build schedule
- Delivery, install, commission, test, train.
The Challenge
This particular automotive client came to us because they needed ‘something like a welding position, but different.’ They needed us to supply a machine used to test the efficiency and effect caused to car engines whilst been turned at obscure angles, in a controlled environment. This would be done to an incredibly (almost unobtainable) high level of precision… and we had to deliver this machine within 2 weeks from date of order! No problem.
Our customer detailed the bespoke, custom built welding positioner and also the unique control panel system they needed. This involved Spectrum designing, building, and supplying a PLC computer control panel connected to the position, and integrated into their plant laboratory computer.
- Attach car engines to the positioner table with custom built jig brackets we designed and manufactured
- Tilt a car engine to near upside angles @ specifically 94° and 127°
- Rotate a car engine into exact positioners with precision control (done from a computer), and turn forward and reverse at high speeds during rotation
- Upgraded RPM
- The tilt gearbox teeth and motor control system had to precision, tight, and to one thousandth mm
- The engine would be running continuously during tilt / after tilt, operating @ full revs
- Monitoring probes and digital sensors to measure engine oil lubrication and fuel efficiency / consumption at obtuse angles
- Engine duty cycle tested and studied
- Control the machine from behind a shatter proof toughened glass screen (that we supplied) in a control booth for protection in the event engines blew up during testing
- Operate from a considerable distance away with a PLC control panel system connected to their computer
- Connect positioner to 34 digital monitoring probes and sensors
- Probes to interact and talk to the positioner tilt and turn system, as well as their computer
- We have done this before with a K-TIG automated system
- AC inverter frequency control tilt motor for variable speed tilt withing microscopic parameters and rapid stop / start control
- We designed and built the positioner control panel and the car manufacturer PLC computer control system, based on the customer’s requirements.
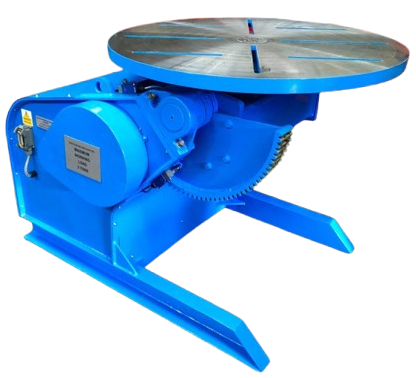
The Solution
Re-design the whole machine. For a lot of clients we have to sign NDA (Non-Disclose Agreements), therefore certain pictures can’t be uploaded. Essentially we took the core frame and functionality of a 3 tonne welding positioner and custom built a new 2-axis handling system, which met the client’s exacting needs for high precision and testing.
This build was quite an extreme case and done in such a short period of time, based on the customer’s quick turnaround requirements. With such demanding parameters for a non-welding related application (whilst connect to and interacting with other measuring equipment) this was seriously challenging. However, after lots of testing (and endless alterations!) we found a way, and it worked perfectly.
This control panel and PLC system was very, very advanced. It was quite interesting to see an old BODE positioner from the 70s turned into a state-of-the-art automotive automation, so we were quite proud to be associated with this particular manufacturer, and honoured to be involved in their production.
Refurbished and Retrofit Schedule
- New AC inverter frequency precision electronic control system
- Digital probes connection points built into the panel and positioner, and installed on site after delivery
- Panel built in accordance with BS EN 7671 18th Edition
- Brand new electronics inc. new cabling and limit switches
- New force-cooled AC motors / braked motors
- New mechanical drive systems
- All re-drilled and tapped
- New EN24T machined parts inc. shafts, keyways, and gears
- New chains
- New tensioners
- New phosphor bronze wear bush sleeves
- New belts
- New pulleys
- New couplers
- New taper locks
- New oil seals and fresh oil
- Shot blasted
- 2 coats of special primer paint (customer specification)
- 4 coats of high quality proprietary blue paint (made to manufacturer’s spec)
- Build, deliver, install, commission, tested. PASS
The result. Happy customer.
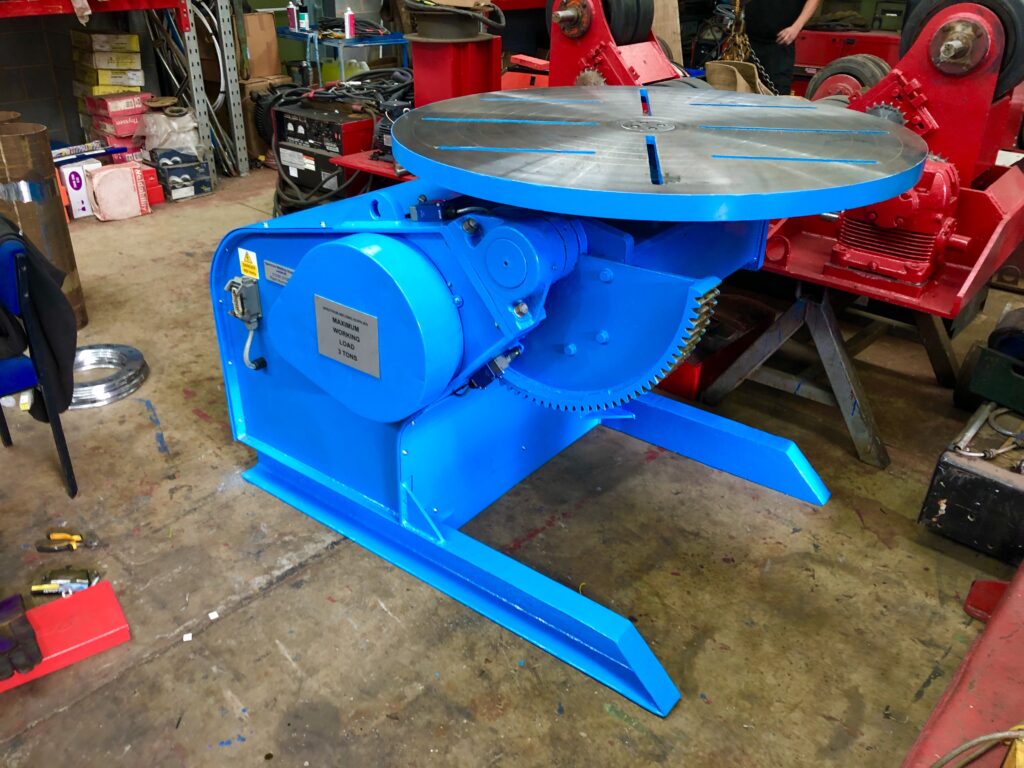
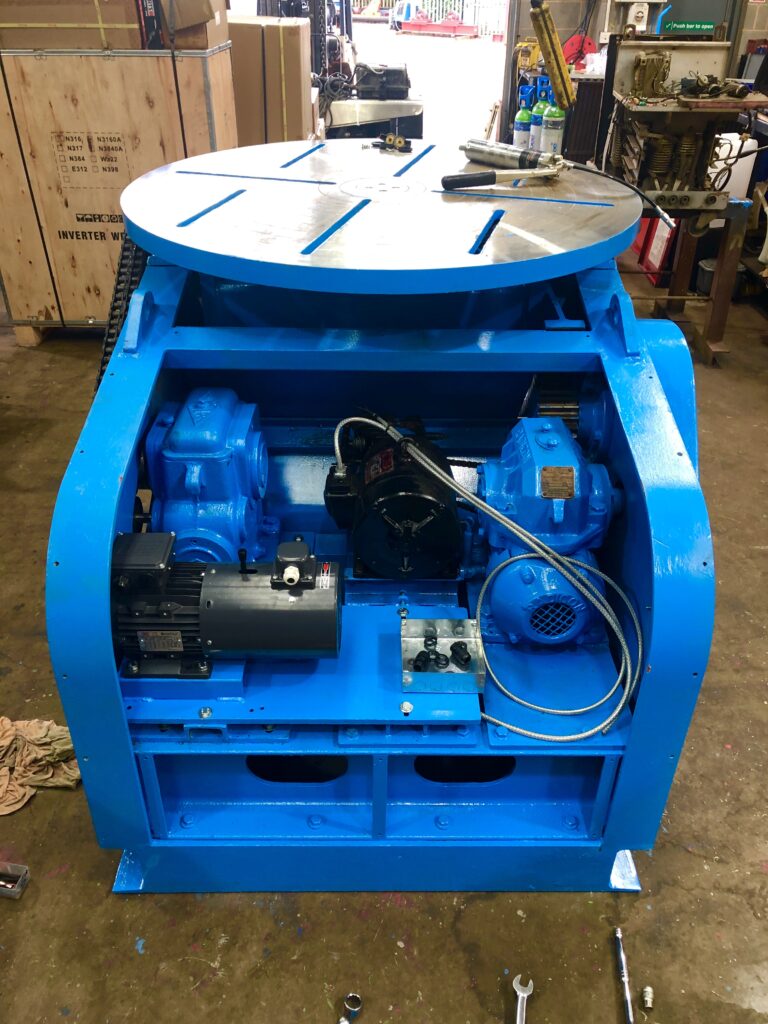
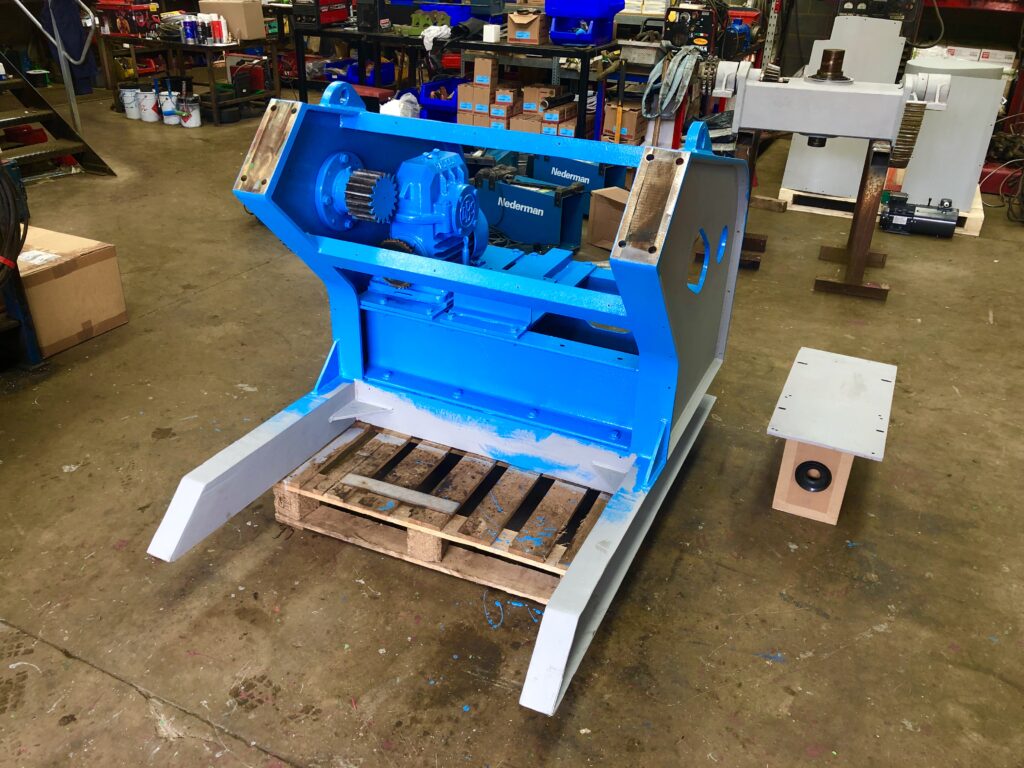
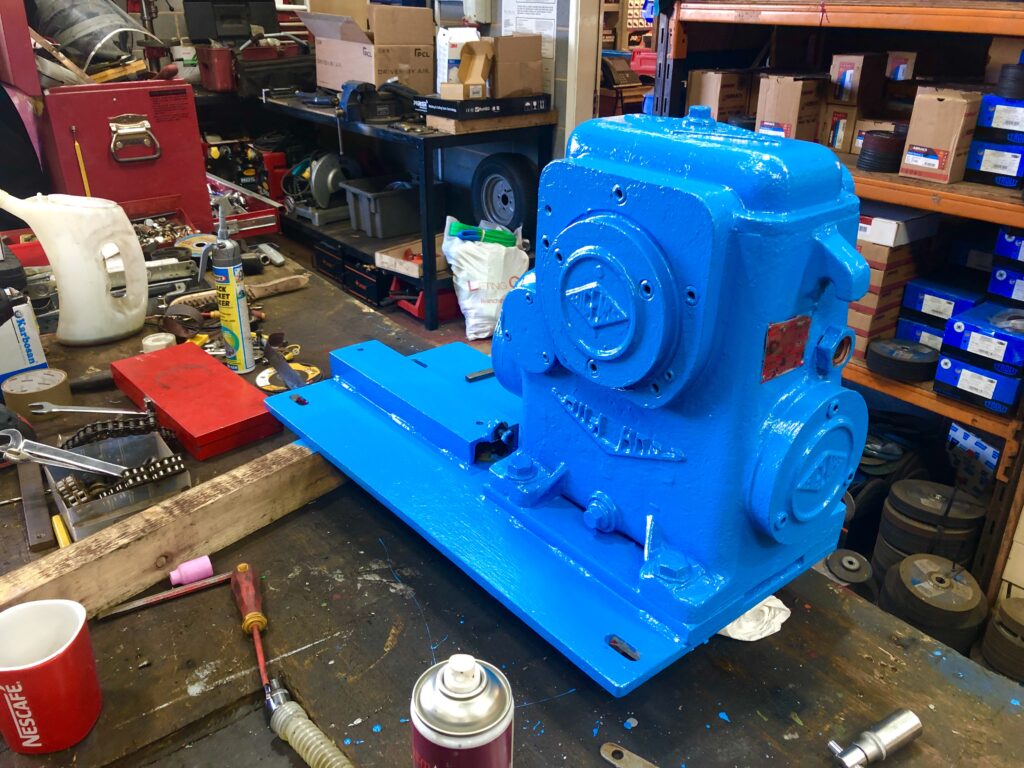
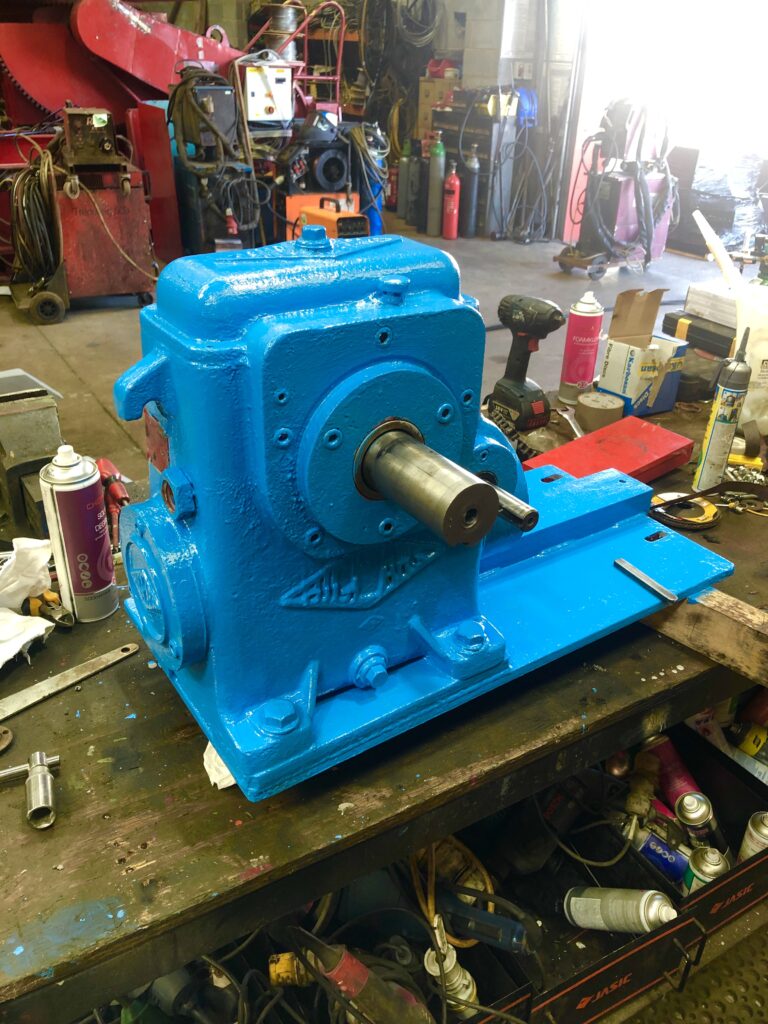
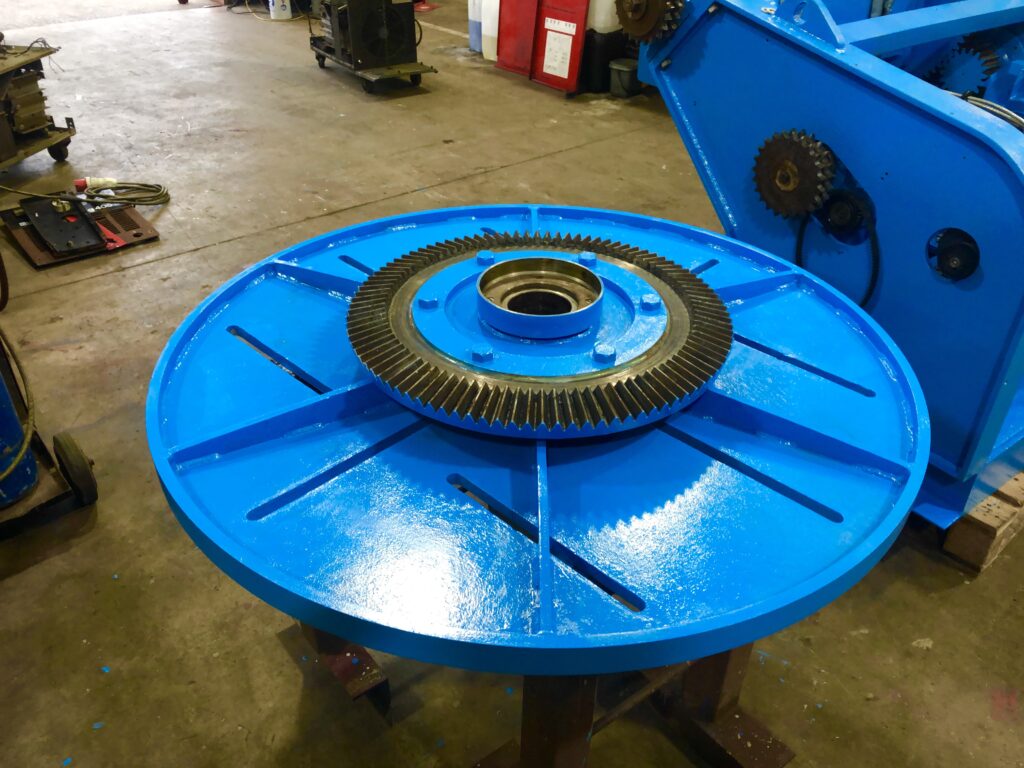
Trusted Support & Warranty
Quality Control
Spectrum Welding are the highest approved supplier and manufacturer in the industry, with LRQA ISO accreditations, BS EN training standards, and much more. We offer full traceability and documentation, with advanced levels of methodical and meticulous attention to detail.
Qualifications
- LRQA ISO 9001
- LRQA ISO 45001
- LRQA ISO 14001
- Trained mechanical engineers designing automated welding system trained to BS EN 62381:2012 (Automation systems)
- Trained to BS EN ISO 13854:2019 (Safety of machinery)
- Trained electrical engineers and control panel wireman to BS EN 7671 18th Edition (Wiring regulations)
- Trained welding plant repair engineers
- 25 years’ experience (42 years in business)
- Trained and coded welders
- 10 years on site as planet repair engineer responsible for all install, commissioning, and training for advanced automated welding systems across the world
- Trinidad and Tobago, Qatar, and more, are the furthest away we’ve supplied to.
- BSI trained
- Prototype model machines delivered to Spectrum for testing and product feedback, before worldwide mass market production
- Familiar with synergic line coding
- 25 years’ experience (42 years in business) supplying automated submerged arc equipment (No.1 in the UK)
- Procedure Qualification Record (PQR) experts
- Owners of all BSI BE EN ISO digital documents
- Calibration competent BSI trained and qualified
- PAT testing trained and qualified
- Fire training qualified
- First Aid trained and qualified
- IOSH (Institution of Occupational Safety and Health) trained
Ongoing support
Aftercare is very important with manufacturing special automation equipment like this. Sometimes we do have to re-attend site after install, as part of ironing out unforseen bugs, glitches, and making adjustments once the job is in motion.
Warranty
With the new equipment and solutions we provide, we offer protection and cover with full warranty included and stated in the quote.
Contact Spectrum for any bespoke engineering projects
Call us any time. We are always available to talk.
Spectrum House
McGregors Way
Turnoaks Business Park
Chesterfield
Derbyshire
Landline: 01246 205267
Joe Fitzpatrick, Managing Director: 07525 101466