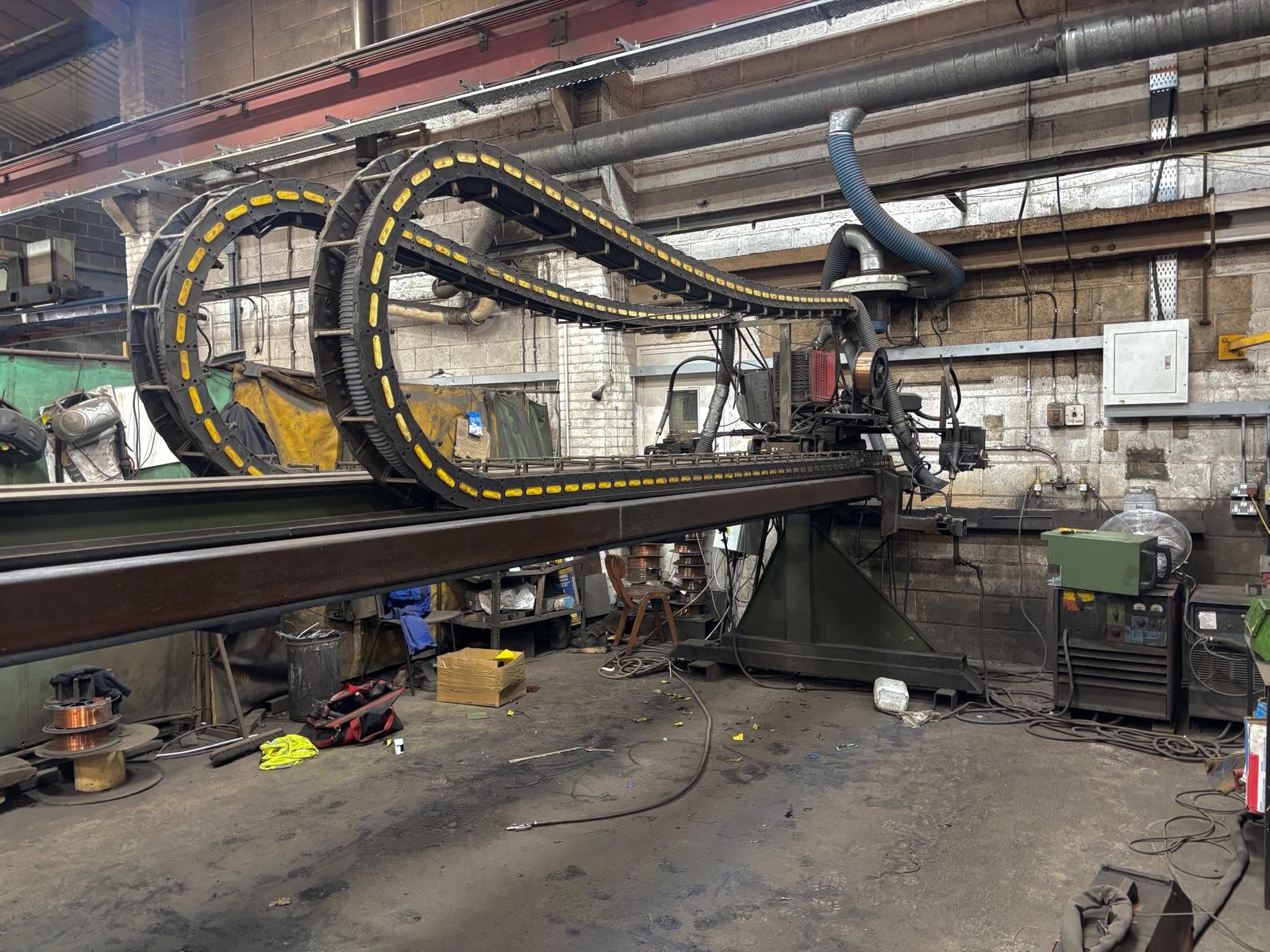
Spectrum upgrade and retrofit seam welder
Refurbishment and retrofitting tandem head MIG seam welder with new drive system
- Discuss client requirements
- Meet the customer
- Site visit
- Problems addressed and solved
- Planning and design
- Specification
- Lead time (back up and running within 4 days from date of order / 2 days downtime)
- Build schedule
- Delivery, install, commission, test, train.
Our customer had a seam welder production line welder in place that MIG welded all day, all night continuously. This was an old seam welder system with cables everywhere, an antiquated motor gearbox, that ended up cutting out and came to grinding halt in a puff of smoke.
We were then approached as a matter of urgency to get our customer’s longitudinal seam welder production line back up and running in the shortest amount of time possible. Our solution was to rip out all the old bogie carriage drive system and replace all of it with brand new the mechanical and electrical 415V motor gearbox components, including much tidier energy drag chain cable carriers for the pendants controllers and LEV fume extraction.
The customer also needed to control the tandem head MIG seam welder from both sides, so we designed a twin pendant system that allow 2 pendants to be attached to the both sides of the seam welder carriage, so the operators could independently control both MIG heads that we setup for 1.0mm solid wire longitudinal seam welds, and the other side with 1.2mm wire seam welds.
Additional safety systems were also needed including forward & reverse traverse limit switches, emergency stops on the control panel and both pendant controllers, and fume extraction ducting connected to powerful fans with fixed nozzles at the welding source.
We also fitted the new 3-phase 415V 32amp MCB D-rated trip dedicated socket and conduit, so the system had a fresh uninterrupted power supply feed.
By being able to offer our customer this automation retrofit repair and upgrade service, we saved them a lot of money not needing to replace this with a new machine with 12 weeks of downtime.
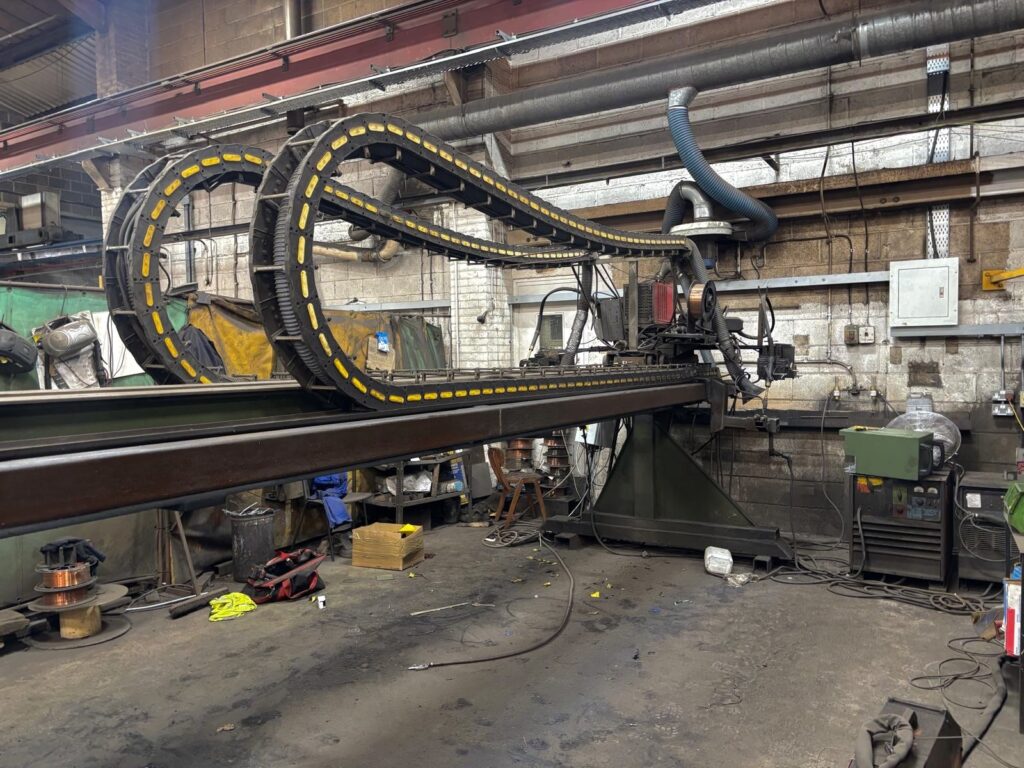
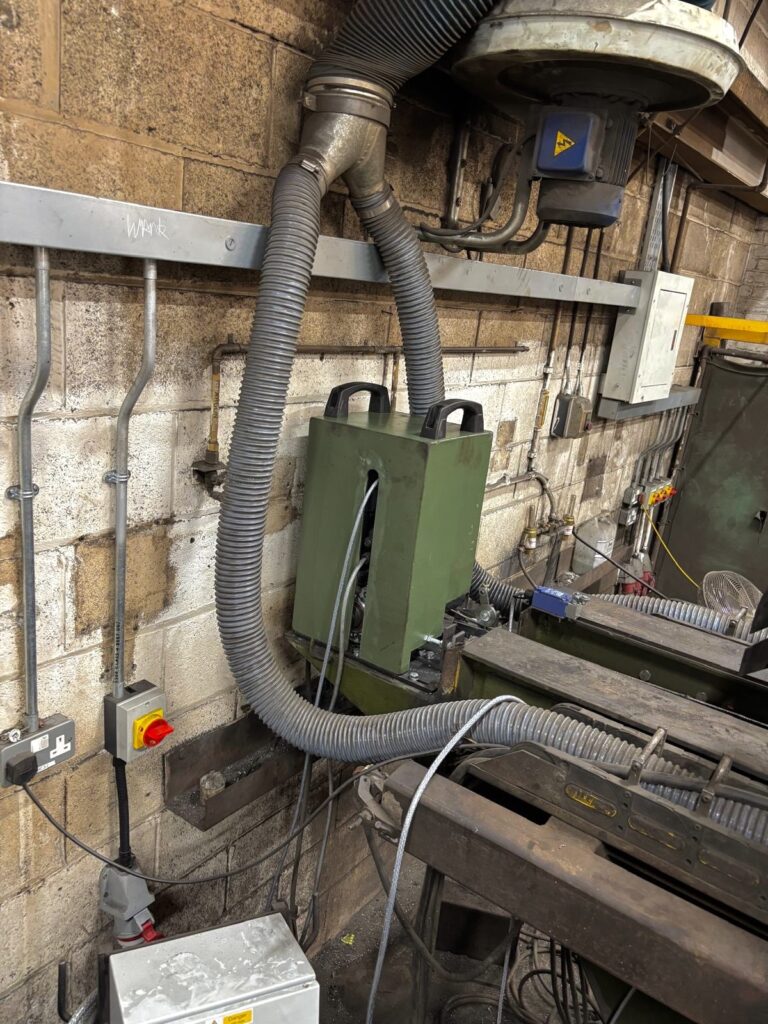
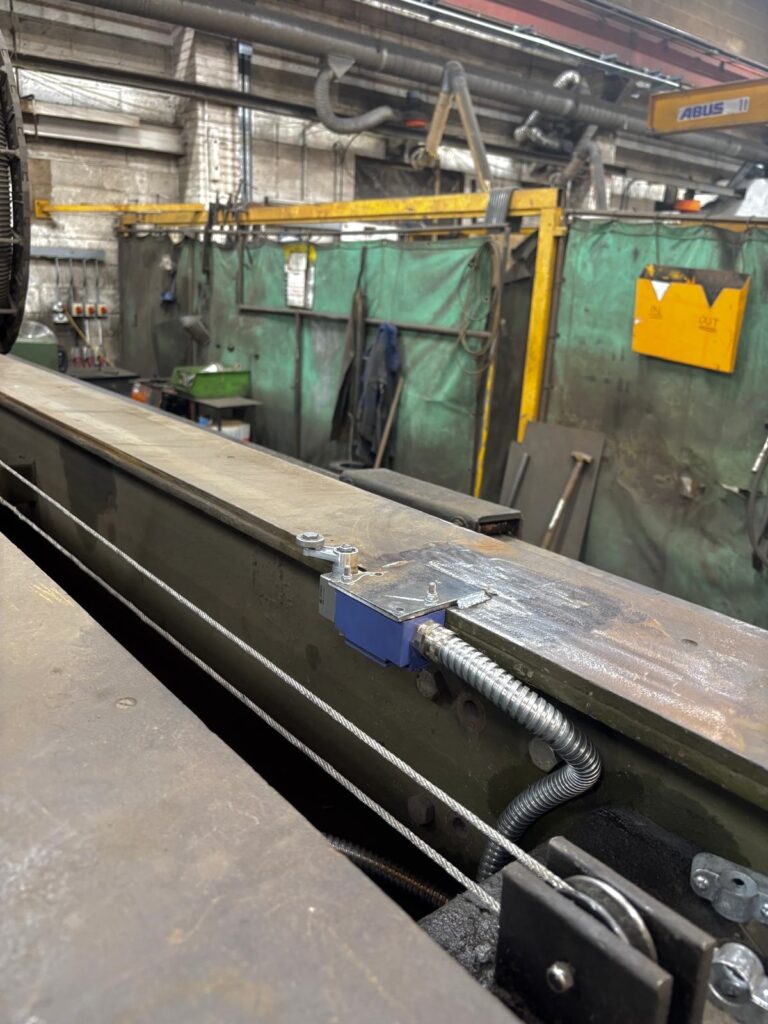
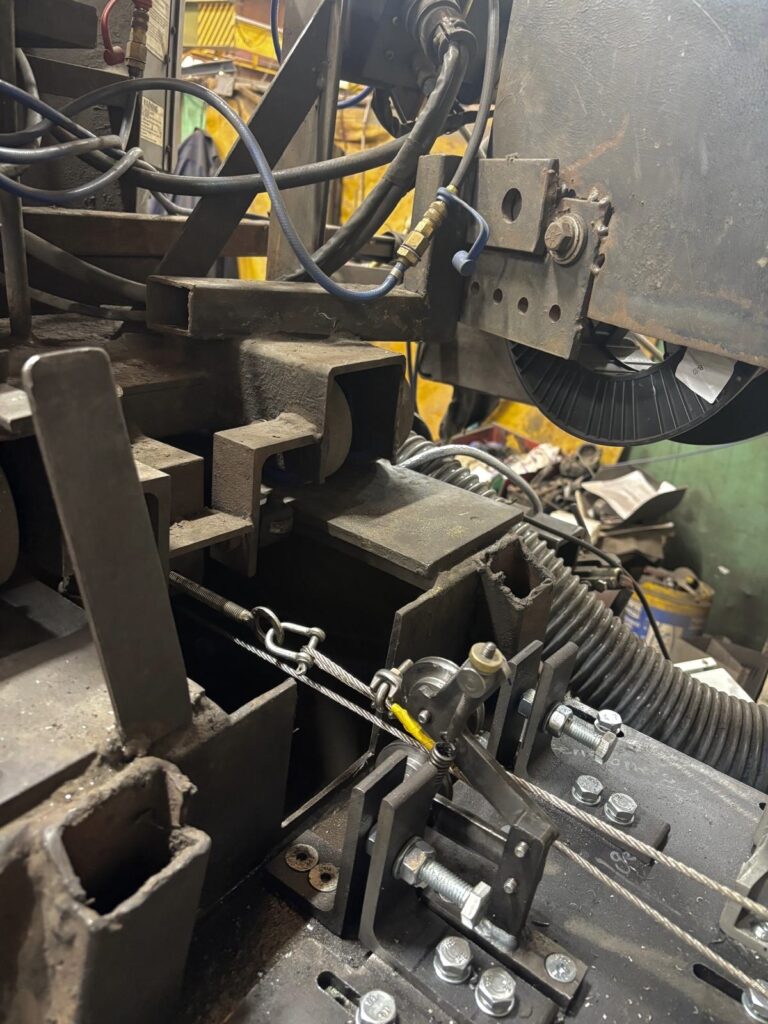
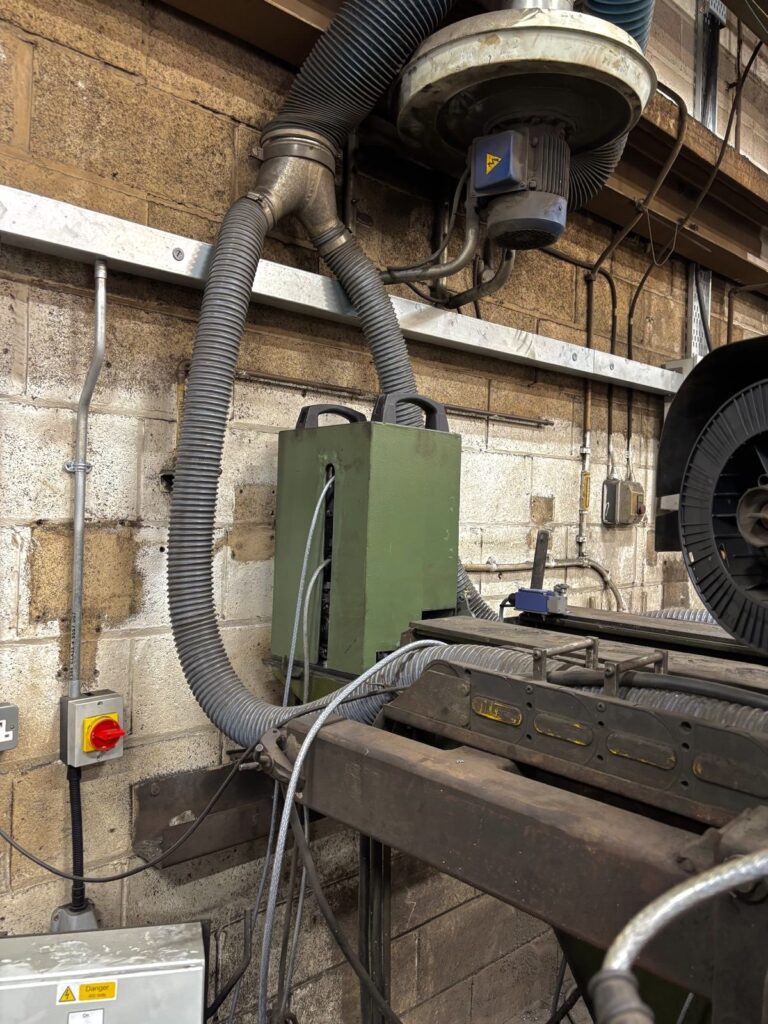
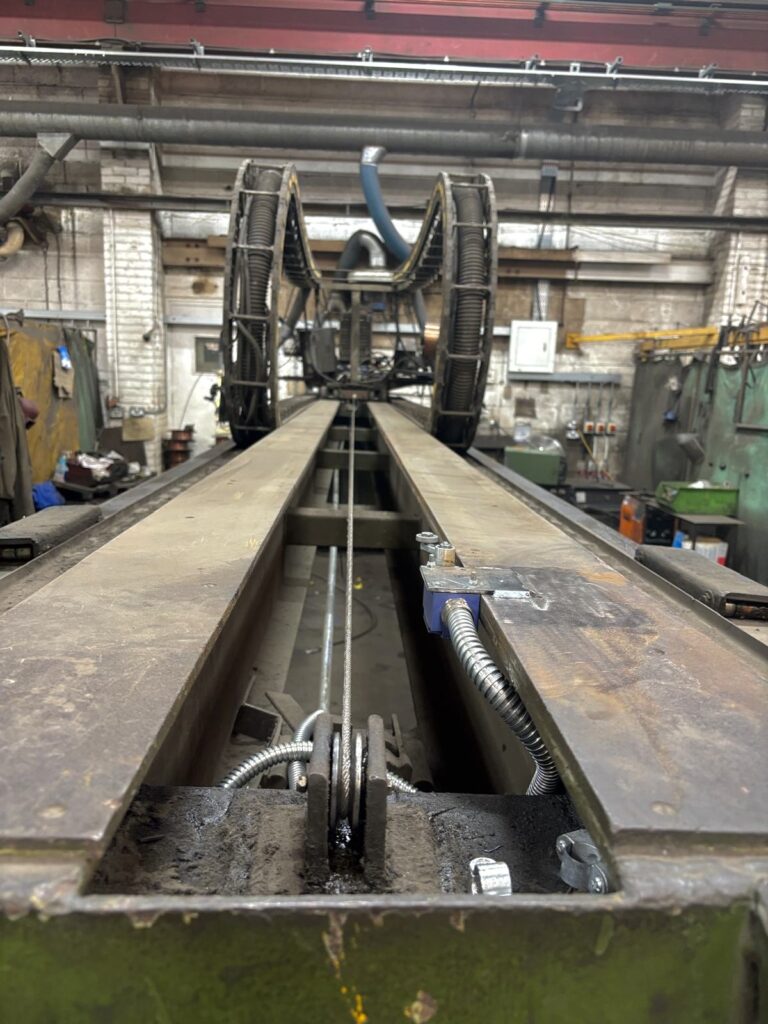
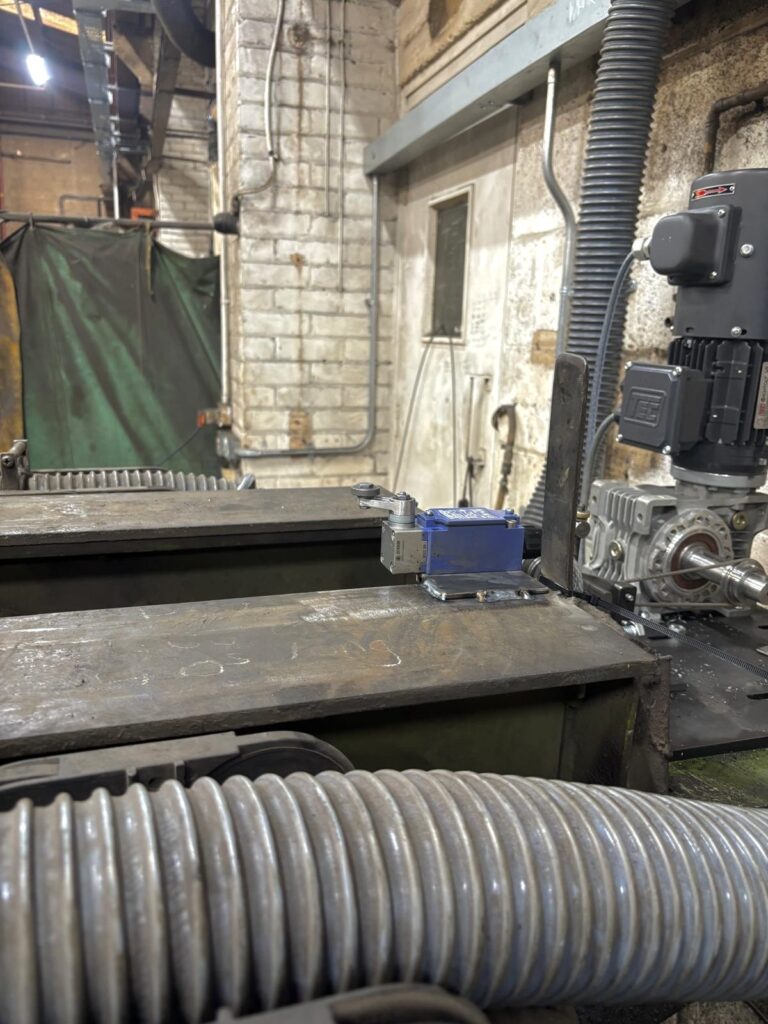
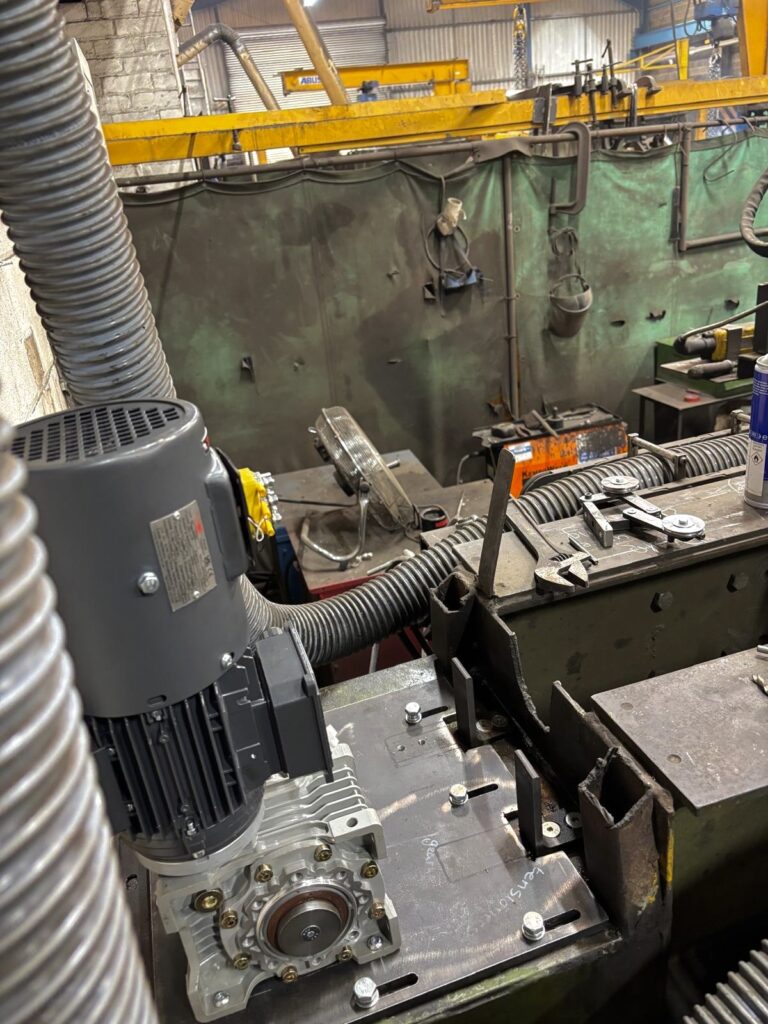
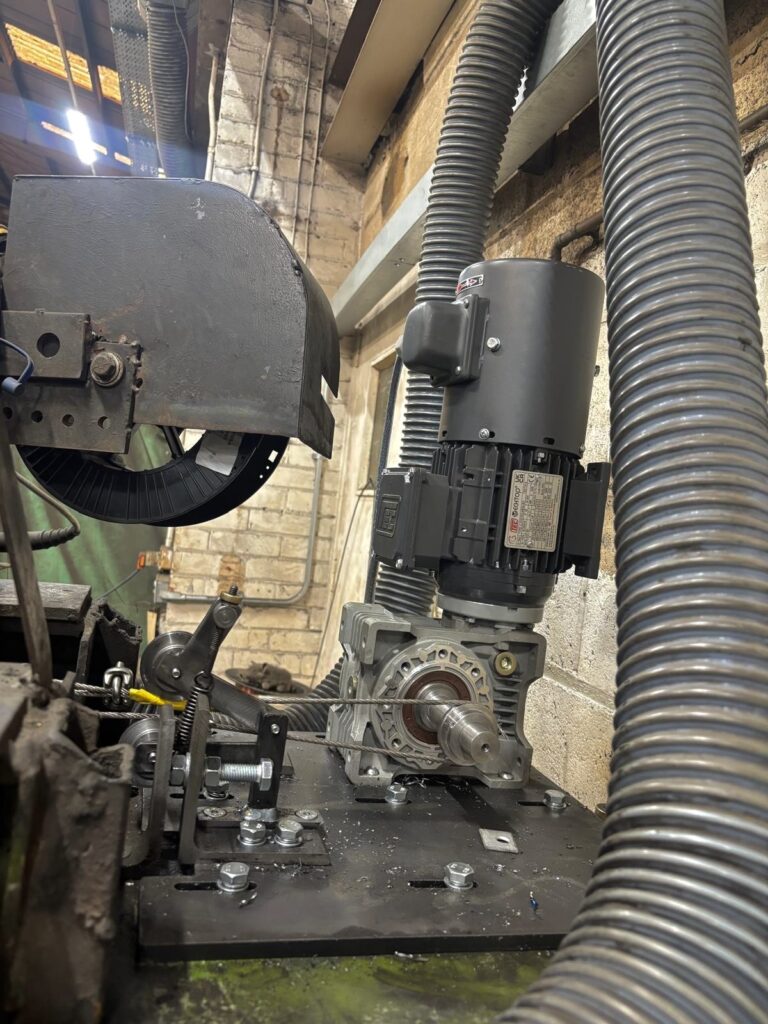
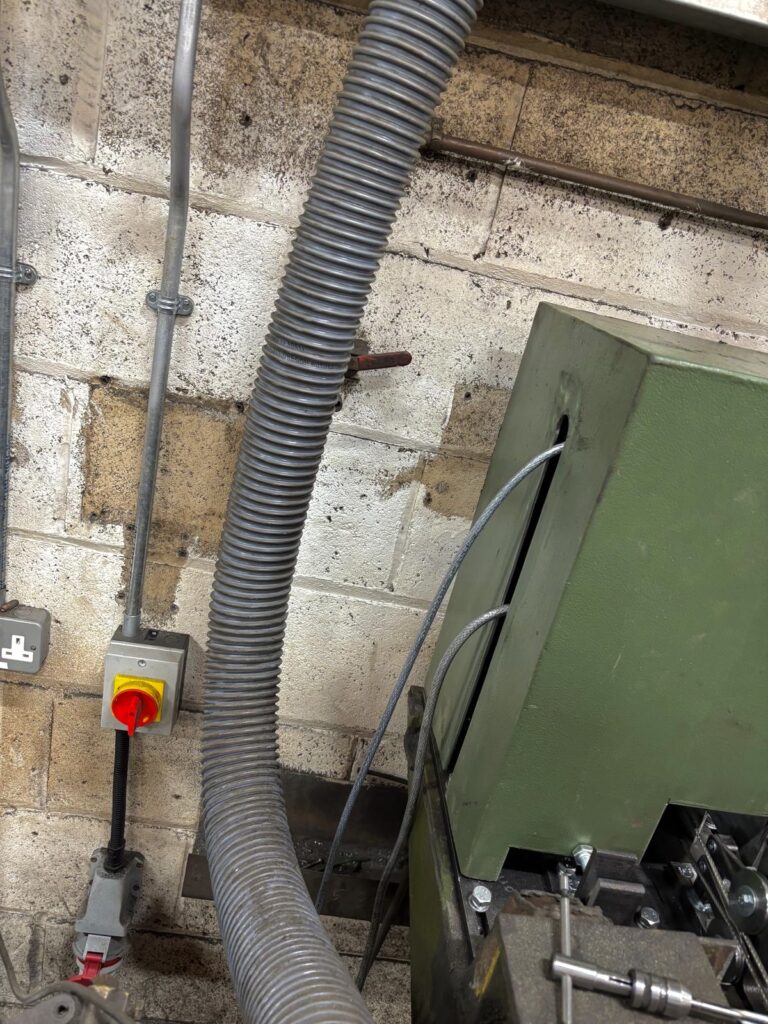
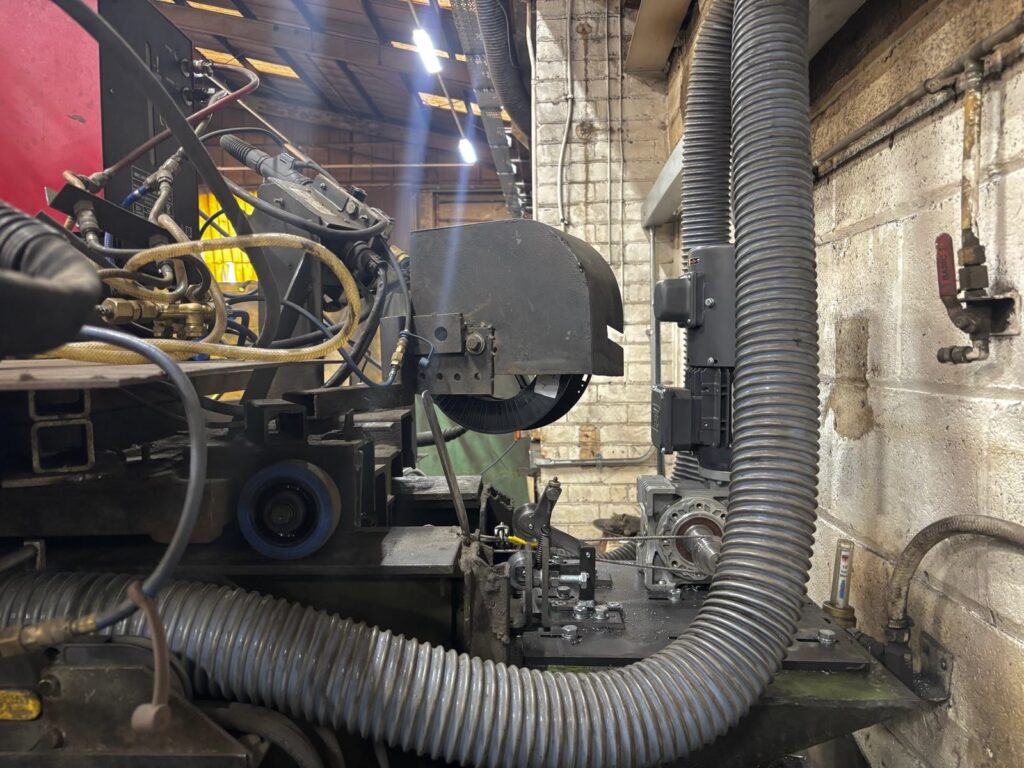
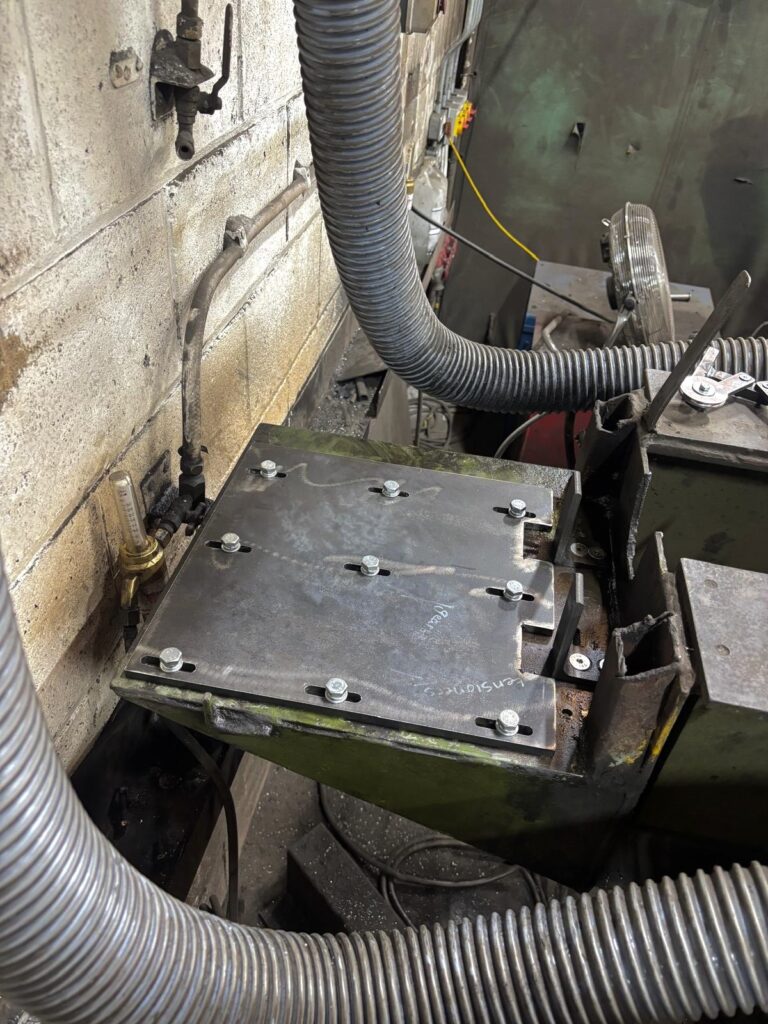
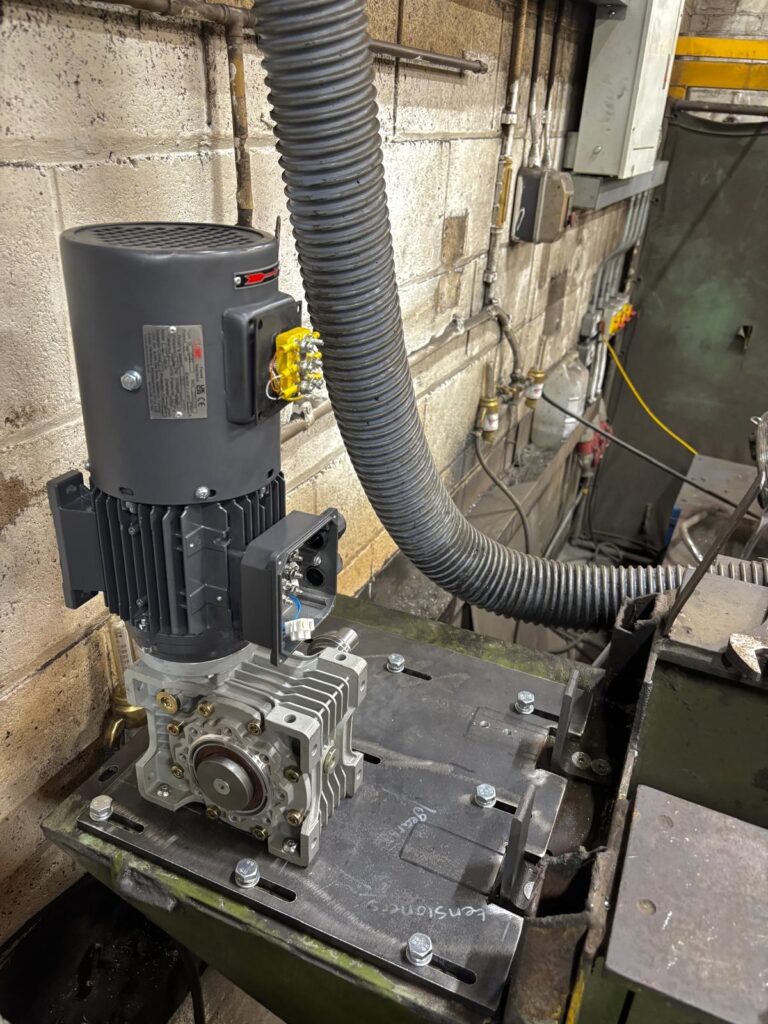
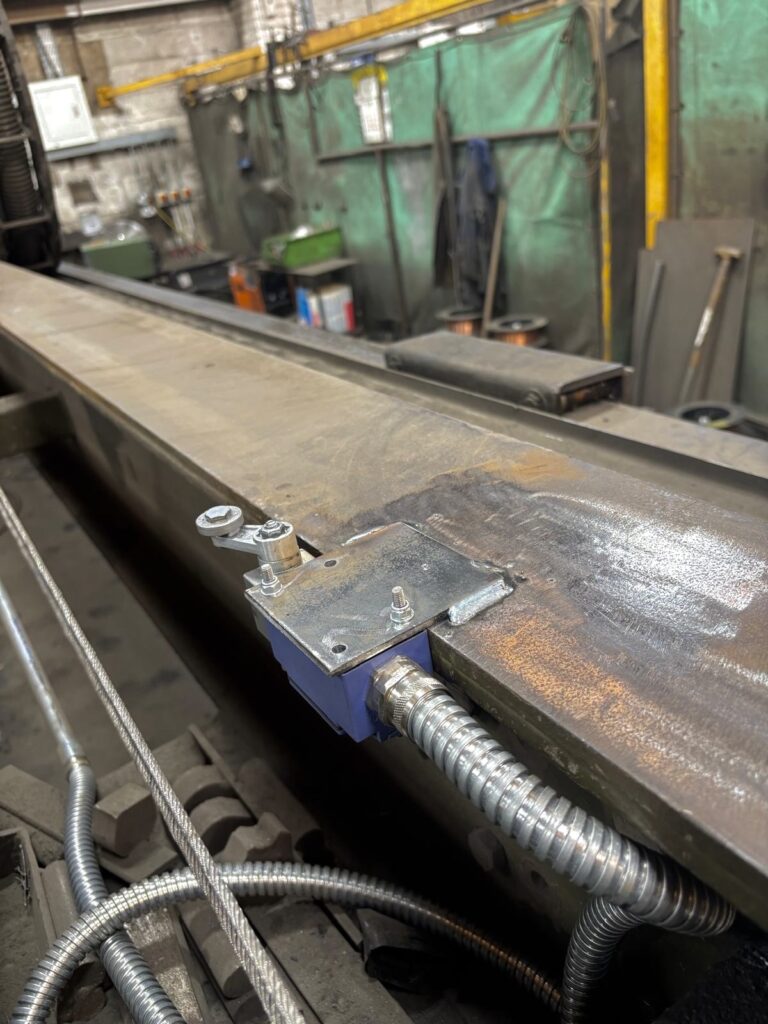
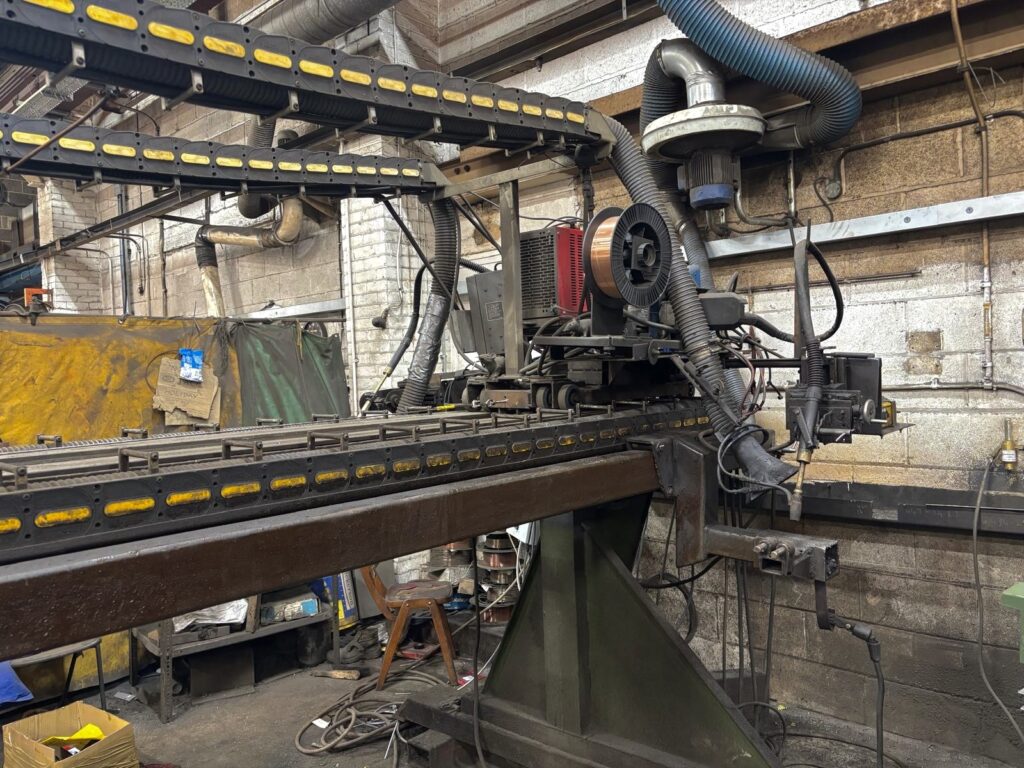
Refurbished and Retrofit Schedule
- New 3-phase AC inverter frequency control system
- New control panel stand
- Panel built in accordance with BS EN 7671 18th Edition
- Brand new electronics inc. all new cabling and new limit switches
- New protective conduit
- New mounting blocked for limit switches
- Drag chain cable carriers fitted to prevent trip hazards (and much neater)
- Fume extraction ducting and system built into design for HSE legislation
- New long cable twin pendant controllers off the same control panel
- Forward / reverse / stop / variable / emergency stop pendant features
- New upgraded more powerful force-cooled AC motor gearbox
- Gearbox ratio, RPM, and torque calculated to meet weld travel speeds
- Motor gearbox 24 hour duty rating efficiency calculated to prevent burnout
- New upgraded and uprated mechanical drive systems
- New wire rope design with pulleys and tensioners
- Pre-existing tandem bogie carriage repaired
- All re-drilled and tapped
- New EN24T machined parts inc. shafts, keyways, and gears
- New CAD drawings with component kN load tolerance calculations
- Shear force calculations
- New tensioner plate and locking system
- New phosphor bronze wear bush sleeves
- New belts
- New pulleys
- New couplers
- New taper locks
- New moving parts cover guards and vents fitted
- 2 coats of special primer paint
- 2 coats of high quality olive green paint (as requested)
- Build, deliver, install, commission, tested. PASS